#185 Addressing Opportunities for Improvement
The ISO Show - A podcast by Blackmores UK - Wednesdays
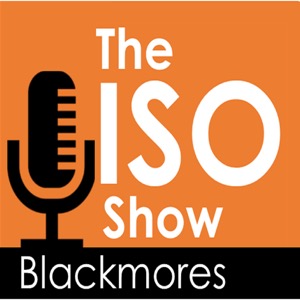
Categories:
Continual Improvement is at the heart of every ISO Standard. The cyclical nature of ISO Standards lends itself to regular review and update of your Management System, to ensure it’s working efficiently and to address any issues or opportunities that inevitably crop up. However, Integrating these improvements can be challenging, even for mature systems. Today Ian Battersby explains the concept of Improvement as defined in ISO Standards, how to find root cause for non-conformities and integrating improvement actions from multiple sources. You’ll learn · What is meant by ‘Improvement’ in ISO Standards? · Common misconceptions about Improvement in ISO Standards · How to address non-conformities in your Management System · Finding the root cause of a non-conformity · Integrating Improvement actions Resources · Isologyhub In this episode, we talk about: [00:30] Join the isologyhub – To get access to a suite of ISO related tools, training and templates. Simply head on over to isologyhub.com to either sign-up or book a demo. [02:05] Episode summary: Ian Battersby will be explaining what Improvement means in relation to ISO Standards, how to address non-conformities and integrating the required Improvement actions. [02:30] What is meant by ‘Improvement’ in ISO Standards? – One of the requirements of all Management System standards is to determine and select opportunities for improvement (Clause 10). This is the fundamental aim of Management Systems: to make things better In the words of the standards, it is so that an organisation can: “Implement any necessary actions to meet customer requirements and enhance customer satisfaction These shall include: a) improving products and services to meet requirements as well as to address future needs and expectations; b) correcting, preventing or reducing undesired effects; c) improving the performance and effectiveness of the management system.” An organisation going through certification for the first time may never have had in place a system for planning improvements. Some organisations are dealing with improvements, but not necessarily through a single, consistent route. While you can meet the requirements of the standards without a single route, the standard is not prescriptive in how you go about this. [04:45] Common misconceptions about non-conformities – the standard does go on to cover nonconformity and corrective action (10.2); is it suggesting these as the main source of non-conformities (NC). It isn’t really explicit about other sources, other than specifically including customer complaints as a form of NC. However, there’s a strong argument for consolidating data from different sources, so it’s worth considering how complaints data is handled. Other sources of non-conformities can include your Internal Audit findings, addressing where you may not be meeting client expectations, addressing failure to meet legal obligations ect. As a reminder, ISO 9000 (Fundamentals and vocabulary) includes the definition of nonconformity: non-fulfilment of a requirement: need or expectation that is stated, generally implied or obligatory i.e. Legal / client expectation. [10:00] Addressing non-conformities – You need to evaluate the need for action to eliminate the cause of the nonconformity, to ensure that the issues doesn’t recur, or pop-up elsewhere. When a non-conformity does occur, you need to: · Determine the causes · Determining if similar nonconformities exist, or could potentially occur; Any corrective actions should be appropriate to the effects of the nonconformities encountered. So, you don’t need to commit a huge amount of resource to minor issues. [11:40] Join the isologyhub and get access to limitless ISO resources – From as little as £99 a month, you can have unlimited access to hundreds of online training courses and achieve certification for completion of courses along the way, which will take you from learner to practitioner to leader in no time. Simply head on over to the isologyhub to sign-up or book a demo. [13:40] Finding the cause of non-conformities – Without removing the cause, repetition may occur, and this is where integrating improvement data from multiple sources comes into its own. The idea of Common cause is - a single cause may manifest itself in very different outcomes. For example, a lack of competence could lead to a process being delivered wrongly, leading to reducing level of quality in service or product, which would be picked up as an NC. Competence is an area which can also lead to NC’s, through the result of a helath & safety incident or environmental incident if people aren’t trained to use equipment or follow set procedures. It can also lead to a customer complaint where the failed process is apparent to a customer. If a product NC isn’t spotted until after the product delivered/in service it could lead to a warranty claim Or even a claim for damages should it lead to harm/loss to the customer It could lead to regulatory breach or even enforcement or legal action Some of these outcomes may not be apparent until they have impacted upon a customer or other interested party, so would not be recorded internally through a nonconformity system. All this to say, finding the root cause will require looking in a lot of different places. Having a common methodology in place to address non-conformities, including considerations for different types of issues, makes life a lot easier. [15:55] Integrating Improvements from multiple sources: There are many sources which can highlight opportunities for Improvement, including: Internal Audit – This is a conformity assessment, so any gaps or issues identified will be NC’s that need addressing. Surveillance Audit / Certification Audit – Your Certification Body will also be conducting a third-party conformity assessment, which may highlight something you’ve missed in your own internal audits. Supply Chain Audit – Auditing your supply chain can also highlight NC’s that you can encourage them to address, both for your benefit and theirs. Client Audit – You may be audited by clients, especially where there may be specific technical industry related issues. Management Review – This is the perfect platform to identify Opportunities for Improvement. You can highlight NC trends from Internal Audits here and define if they need to be addressed separately. You will often have members of senior management present at a Management Review, so there is a greater chance for you to plan tangible actions to address issues, especially if they are business critical. SWOT / PESTLE – This usually happens early on in the Implementation phase, but there’s no reason why you can’t repeat the exercise on an annual basis. This exercise directly identifies your risks and opportunities, both from internal and external sources. Getting input from all levels of staff as they may also shed light on potential NC’s and opportunities other departments may not even be aware of. Accident reporting / Safety observations – Any incident should be viewed as an opportunity to improve. Some accidents are unavoidable, but many are a result of someone not following instructions, equipment being left unattended or in the wrongs location ect. Addressing these will help you to ensure a safer environment. Site inspections – Just walking around your site can yield new insights. Ask other departments that may not visit your area to do a sweep and report any findings. Sometimes all you need is a fresh pair of eyes to highlight issues you’ve missed. Complaint / Other customer feedback – Allow clients and stakeholders to have input. Regulatory requirements – You may discover you are breaching a regulation, which needs to be addressed ASAP. Consider a legal register to keep track of all your legal and regulatory requirements. Enforcement (HSE, EA, professional body) – You may have opportunities for improvement enforced by professional bodies such as the HSE or Environment Agency. Management Action – Any management meetings should take opportunity suggestions from both management and the general workforce. Product NC’s – If you’re in the manufacturing industry, you likely already have a system in place for monitoring any product related non-conformities. This process can be applied on a broader scale, as it embodies the same principles: Identify the problem, find the root cause, address the root cause, put preventative measures in place to stop recurrence. If you’d like to book a demo for the isologyhub, simply contact us and we’d be happy to give you a tour. We’d love to hear your views and comments about the ISO Show, here’s how: ● Share the ISO Show on Twitter or Linkedin ● Leave an honest review on iTunes or Soundcloud. Your ratings and reviews really help and we read each one. Subscribe to keep up-to-date with our latest episodes: Stitcher | Spotify | YouTube |iTunes | Soundcloud | Mailing List