#184 Proactive Hazard Reporting – Consultation and Participation in ISO 45001
The ISO Show - A podcast by Blackmores UK - Wednesdays
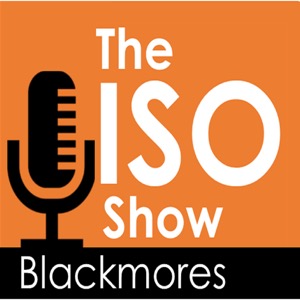
Categories:
In the workplace, everyone is responsible for safety. It’s not just for managers or senior management to worry about where legislation is concerned, everyone from the top to the bottom needs to be actively ensuring the safety of others. ISO 45001 highlights the importance of this in its most recent iteration, which includes a specific requirement for the consultation and participation of workers. But, how does this work in practice? Today Ian Battersby explains what consultation and participation of workers in ISO 45001 is, and how you can incorporate elements of reactive and proactive hazard reporting to meet that requirement. You’ll learn · What is consultation and participation of workers in ISO 45001? · What is the identification of hazards? · What’s the difference between reactive and proactive hazard reporting? · Common approaches to reactive and proactive hazard reporting · Proactive hazard reporting in action Resources · Isologyhub In this episode, we talk about: [00:30] Join the isologyhub – To get access to a suite of ISO related tools, training and templates. Simply head on over to isologyhub.com to either sign-up or book a demo. [02:05] Episode summary: Ian Battersby will be explaining reactive and proactive hazard reporting, and how this relates to the consultation and participation of workers (clause 5.4) requirement in ISO 45001. [02:30] What is ‘Consultation and Participation of workers? – ISO 45001’s clause 5.4 states: “The organization must have a process for consultation and participation of workers at all levels and functions, and their representatives in the development, planning, implementation, performance evaluation and actions for improvement of the OH&S management system.” ISO 45001 expects occupational health and safety aspects to be fully embodied within the organisation structure. All workers should be aware of their responsibilities, and work together to meet the organisation’s health and safety goals. Everyone is responsible for safety. Consultation implies two-way communication, so workers can provide feedback to be considered by the organisation before taking a decision. This is important; the organisation has to consider workers’ feedback before making decisions Participation implies the contribution of workers, including non-managerial workers, to decision-making related to OH&S performance and to proposed changes. [05:50] Hazard Identification – A specific issue which must be considered is the identification of hazards: · Identifying hazards and assessing risks and opportunities (Clauses 6.1.1 and 6.1.2); · Determining actions to eliminate hazards and reduce OH&S risks There are numerous sources for consideration when it comes to hazards · How work is organised · Routine/non-routine activities · Past incidents · Emergency situations · People · Processes · Workplace design · Equipment · Change [07:35] What’s the difference between proactive and reactive hazard reporting? – Proactive is about spotting hazards in advance and putting in place measures to minimise the chances of them materialising and causing harm (eg, through an accident) Reactive is in response to an event which has already occurred, such as an accident; a hazard existed without being spotted already and dealt with. [08:20] A common approach to proactive hazard reporting – Risk Assessment. Consider hazard sources (i.e. people, processes, equipment, workplace etc) and consider what may happen; what could go wrong. Then consider what controls could be put in place to try and prevent that happening. Risk assessment can help you to demonstrate worker consultation and participation by including those affected: · Involved in or affected by an activity · Those delivering a process · Using equipment · Occupying a workplace Those people have valuable knowledge and understanding, sometimes moreso than someone in a supervisory / managerial role. And an absolute must: recording that all employees have read, understand and are committed to the controls included in Risk Assessments; that process may also give rise to workers’ further involvement – through querying, suggesting change etc This also helps the culture of hazard spotting and promotes engagement among the workforce, both of which are vital in driving a proactive approach [11:10] A common approach to reactive hazard reporting: Accident reporting systems is the obvious choice. However, there are ways you can make this more proactive. There are various levels to accident reporting. Traditional systems wait until an accident occurs before recording and acting upon it. Some organisations also record near misses: where an event has occurred, but no harm has been caused. This approach in itself can be very valuable; and it provides an opportunity to act before any harm has occurred. However, we can go a step further and allow the workforce to observe what’s happening; their surroundings and listen to what they feel may present a hazard to them and their colleagues (remember, everyone is responsible for safety). [13:00] Join the isologyhub and get access to limitless ISO resources – From as little as £99 a month, you can have unlimited access to hundreds of online training courses and achieve certification for completion of courses along the way, which will take you from learner to practitioner to leader in no time. Simply head on over to the isologyhub to sign-up or book a demo. [15:30] Proactive hazard reporting in action: Ian recounts his experience in a previous company where their proactive hazard reporting led to meaningful change. This took place in a large manufacturing plant, but there was also significant office-based activity as well. Because of the nature of the work, many people would not have access to online systems so there was both online and paper systems; this is important; if everybody is responsible, everybody needs access and engagement is vital. In addition to the traditional accident/near miss system, there was a safety observation card (all data ended up in the same database). It was simple to fill out, would have only taken about 5 minutes at most. In an organisation of 500ish, we received 2200 observation cards per year by the time I left. When combined with accidents/incidents, there’s a predictable cycle: more reports, poor quality, more accidents, better quality, improved actions, fewer accidents. [17:30] Creating an observation card: It should be easy to understand and record what’s necessary, recommended content includes: · Date / Time · Who was involved – employee / contractor / visitor ect · Location of hazard / incident · Description of hazard / incident (ideally in 10 words or less) You could get more granular and include: · Identification of an unsafe condition or unsafe act · Type of hazard or incident: slip, trip or fall / exit obstructed / machinery being used unsafely / unsafe structure / not using PPE You could also include an option for actions taken if you decide to inform a manager of the issue, if you’ve corrected someone on the use of equipment or PPE ect. [21:15] The Importance of peer inspections: Often they would have supervisors from one area, checking a different one. This fresh pair of eyes may offer new insight into something that you usually miss! Note that you should also encourage any site visitors to do the same. The fact that you’d ask them to report any incident also displays that you take safety seriously, and are open to feedback to improve. [22:40] Hazard scoring: In order to judge that quality, they went a step further and graded all observations from 1-3: 1. Saw something but didn’t act 2. Saw it, acted to put it safe there and then 3. Saw it, acted to prevent it happening again This allowed them to judge how effective hazard spotting is in removing cause and filters out points-scoring. [22:45] The results speak for themselves: Increasing number of observations Increasing number of participants Increasing quality of observations Reducing number and severity of accidents. Over five years, they increased the number of observations per employee ten-fold. As a result, they reduced lost time accidents over 75% This was a superb example of a personal safety campaign and a great demonstration of consultation and participation, It’s not difficult to do, but it needs leadership commitment, constant and clear comms, user-friendly systems and effective analysis / reporting. If you’d like to book a demo for the isologyhub, simply contact us and we’d be happy to give you a tour. We’d love to hear your views and comments about the ISO Show, here’s how: ● Share the ISO Show on Twitter or Linkedin ● Leave an honest review on iTunes or Soundcloud. Your ratings and reviews really help and we read each one. Subscribe to keep up-to-date with our latest episodes: Stitcher | Spotify | YouTube |iTunes | Soundcloud | Mailing List