Creating a More Competitive and Skilled Manufacturing Workforce
PII Podcast - A podcast by Process Industry Informer
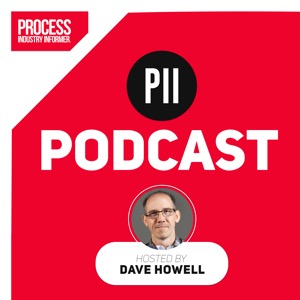
Categories:
In this episode, Shawn Dagley, Kahuna’s Director of Manufacturing, discusses how Kahuna’s data-driven approach to skills management enables leaders to understand their skills supply and demand to make informed staffing decisions in dynamic environments. Kahuna digitises, manages, and validates workforce skill, competencies, experiences, certifications in one platform to increase efficiencies, standardise training and development programs, close skills gaps, mitigate operational risks, increase safety, and guide strategic operating decisions with validated skills insights. From a manufacturing perspective, Shawn and the Kahuna team see four main drivers for establishing a skills-based approach and practice: Worker attainment – There is a severe shortage of manufacturing expertise available in the market today. A well-organised skills management program can help search for the right type of candidate and develop the candidate’s proficiency in the required skills. This method broadens the scope of the job search and improves retention chances within the organisation by supporting development efforts. Worker retainment – Employee satisfaction leads to lower attrition rates. Data shows the average tenure of a manufacturing employee has fallen from 20 years in 2019 to only three years in 2023. With an easily accessible and standardised skills management program, employees have visibility into skills and training requirements, empowering them to own their learning journey within the organisation and shows them the business is invested in their development. Capitalising on the investment in Industry 4.0/Smart Factory – Many companies are investing significantly in I4.0 technologies. Things like Connected Equipment, Additive Manufacturing, Virtual and Augmented reality, Predictive Maintenance. But companies are forgetting to invest in their workforce to maximise the investment in this equipment. Increased product complexity – As products get more complex with the introduction of electronics, software, and AI built in, companies need to expand the capabilities needed in the design and manufacturing of these products. This will drive new skills requirements for teams and individuals. Don’t miss this episode and the opportunity to improve skills management and operational excellence initiatives within your manufacturing environment. Get in touch with Shawn [email protected] Topics include: The key benefits of shifting to skills-based practices in manufacturing How skills management contributes to the efficiency and flexibility of the workforce Why companies struggle with using Excel for skills management How the Kahuna Skills Management Platform works and its core features Real-time visibility into workforce capabilities, and why is this important How skills management supports initiatives like Smart Factories and improves overall equipment efficiency Compliance with quality, safety, and environmental standards How tying compensation to upskilling can increase workforce flexibility Success story of a client who significantly benefited from implementing Kahuna’s skills management system Integrating with other systems like Core HRIS, Learning Management Systems, and Planning & Analytics tools What the first steps are transitioning to a skills-based management system